Metallography - Introduction
How to show the microstructural characteristics of metal and alloy materials
Dionis Diez
Leica Microsystems
Metallography is a discipline that studies the microstructure of various metal alloys, which can be more accurately defined as the scientific discipline for observing and determining the chemical and atomic structures, spatial distributions, inclusions or phases of metal alloys. Broadly speaking, these same principles can be applied to the characterization of any material.
Different technical means can be used when displaying the microstructure characteristics of the metal. Most investigations are performed using the incident light microscopy technique in bright field mode, while other less common contrast techniques, such as dark field or differential interference (DIC), and color (tone) etching, are being The field of metallography applications expands the range of use of optical microscopes.
Many important macroscopic properties of metallic materials are highly sensitive to microstructure. Important mechanical properties, such as tensile strength or elongation, as well as other thermal or electrical properties, are directly related to the microstructure. Understanding the relationship between microstructure and macroscopic properties plays a key role in the development and manufacture of materials and is the ultimate goal of metallography.
As far as we know, metallography is largely due to the contributions of the 19th century scientist Henry Clifton Sol, who pioneered the research on steel made by Sheffield (UK) using modern technology, highlighting The close relationship between microstructure and macroscopic nature. Before his death, he said: "In the early days, if a railway accident occurred, I would advise the company to take the rails and use the microscope. Because of this suggestion, I was considered the best person to deal with such problems. However, at present This measure has become very common..."
Long time but important
With the new developments in microscopy and the recent use of computers, metallography has become a valuable tool for scientific and industrial advancement over the past 100 years.
In metallography, the correlation between the earliest established microstructure and macroscopic properties using optical microscopy includes:
Reduced grain size, overall increase in yield strength and hardness
Anisotropic mechanical properties and elongated grains and/or preferred grain orientation
Increased inclusion content and overall decline in ductility
Direct influence of inclusion content and distribution on fatigue crack growth rate (metal) and fracture toughness parameters (ceramics)
Correlation of the starting site of the fault with material inhomogeneities or microstructure features, such as second phase particles
By examining and determining the amount of material microstructure, you can better understand its performance. As a result, metallography can be used in almost all phases of the life of the component: from initial material development to inspection, production, manufacturing process control, and failure analysis (if needed). The principle of metallography helps to ensure the reliability of the product.
Figure 1: Pearlite gray cast iron
Established and intuitive approach
Analysis of the microstructure of the material helps to determine if the material has been processed correctly, and as such, it is often an important issue in many industries. The basic steps of proper metallographic examination include: sampling, sample preparation (slice and cutting, mounting, plane grinding, roughing and polishing, etching), microscopic observation, digital imaging and recording, and extraction by stereology and image analysis. Quantitative data. Zhongxian Hengye (Hong Kong) Co., Ltd. / Beijing Zhongxian Hengye Instrument Co., Ltd. is a professional provider of optical microscopes. The company has a registered capital of 5.01 million yuan. It has marketing service centers in Beijing, Hong Kong and Zhengzhou. It has the qualifications of medical device management enterprises. It can operate Class II and Class III medical device products according to law. In 2013, the company obtained import and export rights. And national 3A-level corporate credit qualifications. Customers include agriculture, forestry, medical, aerospace, aviation, marine, military, machinery, metallurgy, electric power, petrochemical, geological and other industries, in institutions of higher learning, research institutes, life sciences, industrial materials, medical and health, agricultural systems, livestock systems, The military system and other fields have considerable visibility and influence. Zhongxian Hengye is an agent of the internationally renowned optical manufacturer Leica Optical Microscope.
The first step in metallographic analysis: sampling, which is the key to the success of any subsequent study: the sample to be analyzed must be representative of the material being evaluated. The second step is equally important, that is, the correct preparation of metallographic samples, there is no unique way to achieve the desired results.
The metallography has traditionally been described as both a science and an art. The reason for this is that the experience and intuition used to display the true structure of the material is equally important and must not cause significant changes and damage to display and present measurable specialty.
Etching is the most likely step to change, so careful selection of the best etch composition and control of the etch temperature and etch time are necessary to obtain a definitive and retestable result. Multiple attempts and incorrect experimental methods are required to find the best parameters for this step.
Not just metal
Metals and their alloys still play a prominent role in the development of various technologies because they offer a wider range of properties than any other group of materials. The number of standardized metal materials has expanded to tens of thousands and is constantly increasing to meet new requirements.
However, with the evolution of technical specifications, ceramics, polymers or natural materials have been covered in a wider range of applications, and metallography has expanded to include new materials from electronics to composites. The term "metallography" has now been replaced by the more general "materials" for the treatment of "ceramic phase" of ceramics or "plasticity" of polymers.
In contrast to metals, high performance or design made ceramic articles have higher hardness values, even if they are fragile. Other outstanding properties include excellent high temperature performance and good wear resistance, oxidation resistance or corrosion resistance in harsh environments. However, all the advantages of these materials are affected by chemical composition, impurities and microstructure.
Similar to metallographic preparation, the preparation of ceramic samples for microstructural studies requires multiple steps, but each step requires careful selection of parameters and must be optimized to ensure that it is not only suitable for all types of ceramics, but also for special grade. The inherently fragile nature of these materials allows them to be replaced with diamonds in the various steps of the preparation, from the final polishing of the cutting blades. Etching is a challenging step due to the chemical resistance of ceramics.
Beyond Mingfield
For decades, optical microscopy has been used to gain insight into the microstructure of materials.
Brightfield (BF) illumination is the most commonly used illumination technique in metallographic analysis. In the bright field of incidence, the light path comes from the light source, passes through the objective lens, is reflected on the surface of the sample, and is returned through the objective lens, and finally irradiated to the eyepiece or camera for observation purposes. Since a large amount of incident light is reflected on the objective lens, a bright background is produced on the plane, and when the incident light is dispersed and reflected at various angles or even partially absorbed, the non-planar surface appears dark, such as cracks and fine holes. The corroded grain boundary is characterized by a significant reflectance, such as a precipitate on the surface and a second phase inclusion.
Dark field (DF) is a little-known but effective lighting technology. The optical path of the scotopic illumination passes through the outer hollow ring of the objective lens, illuminates the sample at a high angle of incidence, reflects on the surface, passes through the interior of the objective lens, and finally illuminates the eyepiece or camera. This type of illumination causes the plane to appear dark, since most of the light reflected at high angles of incidence does not pass through the interior of the objective lens. For samples that occasionally exhibit non-planar features, such as cracks, pores, and corroded grain boundaries, the dark-view image shows a darker background that is brighter than non-planar features and emits more light onto the objective.
Bright field: Only direct light is incident on the surface of the sample, where light is absorbed or reflected. The image quality parameters are brightness, resolution, contrast, and depth of field.
Dark field: Light that is only refracted, diffracted, or reflected is incident on the surface of the sample. The dark field is suitable for all samples with structured surfaces and the structure can also be observed below the resolution limit. The surface structure can appear bright on a dark background.
Differential interference difference (DIC), also known as Nomarski contrast, helps to observe small height differences on the surface of the sample, thereby enhancing contrast characteristics. The DIC uses a Wollaston prism with a polarizer and an analyzer with the drive shafts perpendicular to each other (intersecting at 90°). The two light waves split by the prism interfere with the surface of the sample and exhibit a visible height difference and a change in color and texture.
In most cases, incident light microscopy can provide the most information you need, but in some cases, for specific polymers and composites, transmission light microscopy (for transparent materials) and the use of dyes or dyes can An in-depth observation of the microstructure is achieved, and when three standard sample preparations and normal incident illumination are used, the microstructure of the sample cannot be observed.
Since many thermoset materials are inert to common metallographic etchants, the microstructure of the sample can typically be observed using transmitted polarized light to enhance the refractive index difference of discrete features.
Polarization: Natural light consisting of light waves and any number of vibration directions. The polarizing filter allows only vibrating light waves parallel to the direction of transmission to enter. The two polarizers intersect at 90°, producing maximum extinction (blackening). If the sample between the polarizers changes the direction of vibration of the light, a color having birefringence characteristics appears.
Differential Interference Difference (DIC): The DIC method can observe height and phase differences. Wollaston prisms differentiate polarized light into ordinary and special light waves. These vibrating waves intersect at right angles and propagate at different rates and are separated from each other, which allows a three-dimensional image of the surface of the sample to be obtained, although true topographical information cannot be obtained from the image.
Life is colorful
The natural color use of microstructures is often very limited in metallographic applications, but when using certain optical methods, color can reflect useful information, such as polarized light or differential interference, or sample preparation methods, such as Color etching.
Polarizing microscopes are useful for examining non-cubic crystal structures such as titanium, tantalum, uranium, and zirconium. Unfortunately, the major commercial alloys (iron, copper, and aluminum) are not sensitive to polarized light, so color or tone etching provides an additional means to display and identify features of the microstructure.
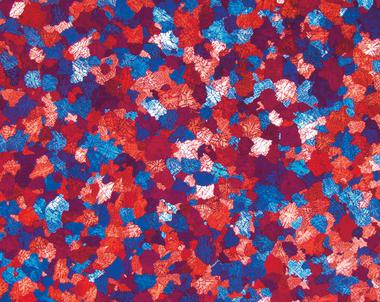
Figure 2: Dendritic colored particles
Color (tone) etchants are typically performed using chemistry (soaked in solution) or electrochemically (immersed in a solution with electrodes and applying electricity) and produce a film on the surface of the sample, which typically depends on the characteristics of the object. The film interacts with the incident light and produces color by interference, which can be observed by normal brightfield illumination, but can be greatly enhanced by polarized light and phase retardation (λ slices or wave plates). In addition, thermal or vapor deposition is another method of creating interference films.
In the steel alloy, a component called "second phase" can be selectively colored by etching, thereby providing a method for distinguishing and quantifying the above components. It is a common method to identify ferrite and carbide in steel by color etching.
The growth of the interference film can produce crystal orientation features such as particles on the surface of the sample. Alloys etched using standard reagents (interfering with grain boundaries) create incomplete networks (grain boundaries) and thus prevent digital image reconstruction, which ensures the particles to be processed due to the different particle orientations Size is analyzed.
Quantitative is better than qualitative
The root of quantitative metallography lies in the application of optical microscopy to achieve the purpose of studying the microstructure of metal alloys. The first basic problem that material scientists must address is:
What is the size of some features in the alloy and how many types of features are there?
How many special components are there in the alloy?
Figure 3: Spherical graphite cast iron (HC PL Fluotar 10x objective, bright field).
The use of chart ratings and visual comparisons over the years is the only way to explain such problems in a semi-quantitative manner. Today, modern electric and computer microscopes and image analysis systems provide a fast and accurate method for most automated evaluation and evaluation methods covered by international or industry standards.
Measurements are typically taken on a series of two-dimensional images, and measurements can be divided into two groups: one for quantifying the size, shape, and distribution of discrete particles (feature measurements) and the other for matrix organization (field measurements) ).
Some examples of the first group include steel inclusion content, graphite classification in cast iron, and porosity evaluation in thermal spray or sintered parts.
Common areas of application for field of view measurement include the determination of the average grain size by means of interception or planar measurement, and the evaluation of the volume fraction of the microstructure components by phase analysis. Using image analysis software, multiple phases in a single field can be detected and quantified, and finally the results of the analysis are presented graphically.
Both microscopic and macroscopic
Macroscopic inspection techniques are often used in routine quality control and failure analysis or research. In general, the preparation of these techniques is done using a microscope, but sometimes it is considered a standard for acceptance or rejection.
Figure 4: Surface hardening of steel.
Macro-etching inspections may be the tools that provide the most informative information, and are widely used in quality inspections at many stages of material processing or forming. With the use of stereo microscopes and a variety of lighting techniques, macro-etching can show uneven distribution of material microstructures, providing an overall view of component uniformity. Here are a few examples:
Macrostructure pattern due to solidification or work (growth mode, streamline, banding, etc.)
Penetration depth and heat affected zone
Physical interruptions (pores and cracks) due to curing or work
Chemical and electrochemical surface modification (decarburization, oxidation, corrosion and contamination)
Surface hardening of steel alloys due to non-compliance of quenching (surface hardening)
Damage caused by improper grinding or processing
Thermal effects due to overheating or fatigue
Bedside Cabinet,Abs Hospital Cabinet,Abs Patient Cabinet,Hospital Bedside Locker
Jiangmen Jia Mei Medical Products Co.,Ltd. , https://www.jmjiameimedical.com